ローラーコンベアピッキングシステム
Roller conveyor picking system
01Feature
ローラーコンベアで作業員の負担軽減
物流作業の一業態として90店舗への仕分け&配送業務を行ってきたが、作業員の負担の軽減・スピードアップ・正確性の向上を目指して、新たにローラーコンベア・ハンディターミナル・自動ラベル発行機器を用いたシンプルなピッキングシステムを構築した。
02Feature
特 徴
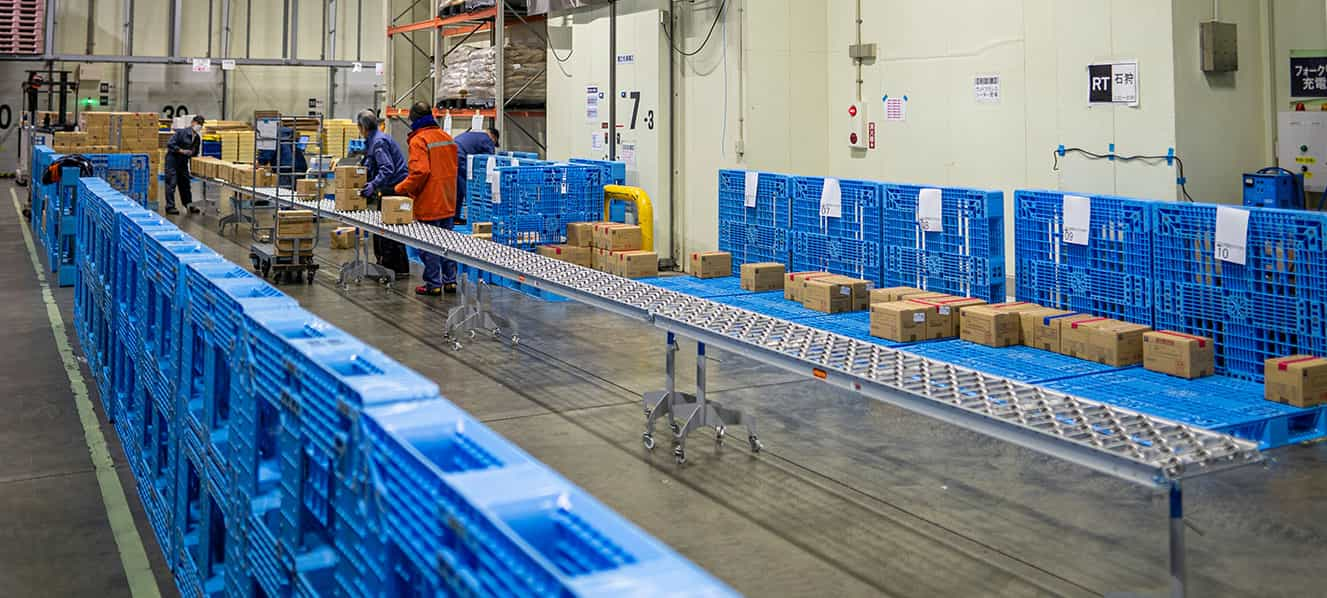
遂行する業態は90店舗・260アイテム・約2000ケースを仕分けするもので、管理者がピッキングリストを見ながら店舗名・ケース数を口頭で指示し、指示を受けた作業員が該当商品の該当ケース数を店舗仕分けエリアへ格納する作業を行っていた。店舗数が多いため、動線が長く出発後に再度店舗名やケース数を確認するなど効率的な作業とは言えない状態であった。また、類似店舗名称も多く仕分けミスも一定数あったことから、新たにシステム構築を行うべく調査を行った。
業態の特徴としては、全て中継からのケース出荷で、外装ダンボールにバーコードが印字してある。また、前述の通り店舗数が多くて動線が長いため、一店舗ごとのケース数が多い時は一度ドーリーや長台車へ積み替えた上で店舗別仕分けエリアへ移動するなど、作業員の負担が大きくなっていた。
作業員への負担軽減をメインに考え、動線短縮に効果の大きいローラーコンベアを用いることとした。また、全アイテムにラベルを貼付してその後の作業でのわかりやすさを担保し、類似店舗名称対策としては店舗番号での仕分けへと切り替えることによりミス軽減を狙った。
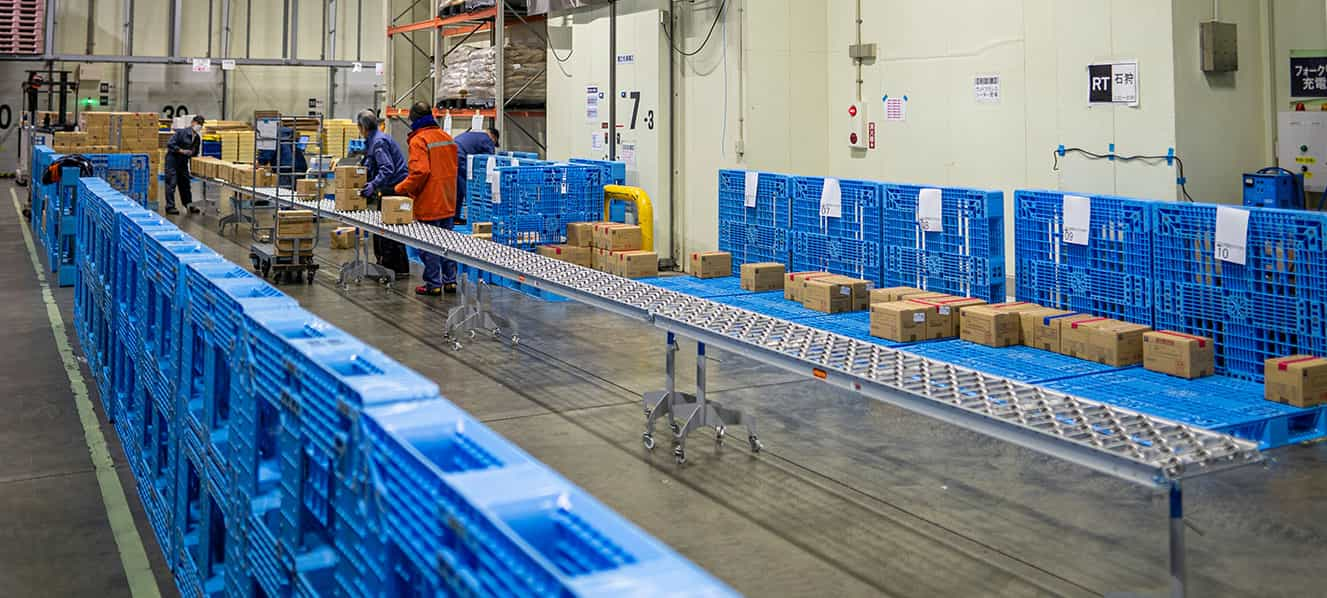
03Introduction
導 入
使用する機器 / システム機器は全て無線対応とし、作業場所の移動にも柔軟に対応できる。
- ローラーコンベア(3m×6本)
- ノートPC(無線LAN対応)
- ハンディターミナル(orリングスキャナ):ノートPCに接続
- ラベルプリンタ(剥離方式・無線LAN対応)
- ノートPCとラベルプリンタの可動式置き台
ピッキング作業 / 下記、1〜5を繰り返し行って仕分け作業を行う。
- 1.作業員A(1名)がパレット積みの商品をアイテムごとローラーコンベアに乗せる。
- 2.作業員B(1名)がローラーコンベア上の商品を順番にバーコードスキャンする。
- 3.作業員Bがバーコードスキャンをトリガーとして発行されたラベルを商品に貼る。
- 4.作業員Bがラベル貼付済みの商品をローラーコンベア後続のラインへ押し出す。
- 5.作業員C(複数)が商品ラベルの店舗番号を読み、該当する店舗エリアへ格納する。
※数量や店舗の確認を現場ノートPC上で行うことができる。ラベル再発行も画面操作で発行することが可能。
03Feature
各機器及びシステムの特徴
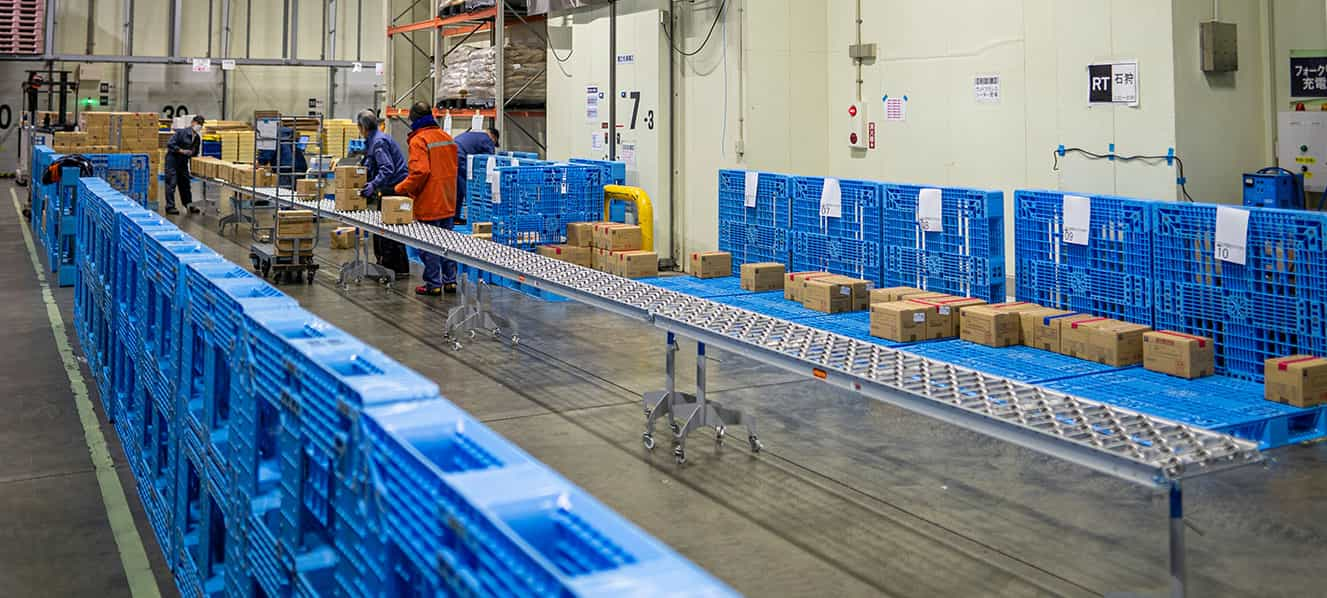
01.ローラーコンベア
3mのローラーコンベア6本を作業動線短縮を目的に導入。汎用品のため、今後の追加要望にも柔軟に対応可能。これだけでも作業員の作業動線が格段に減少した。
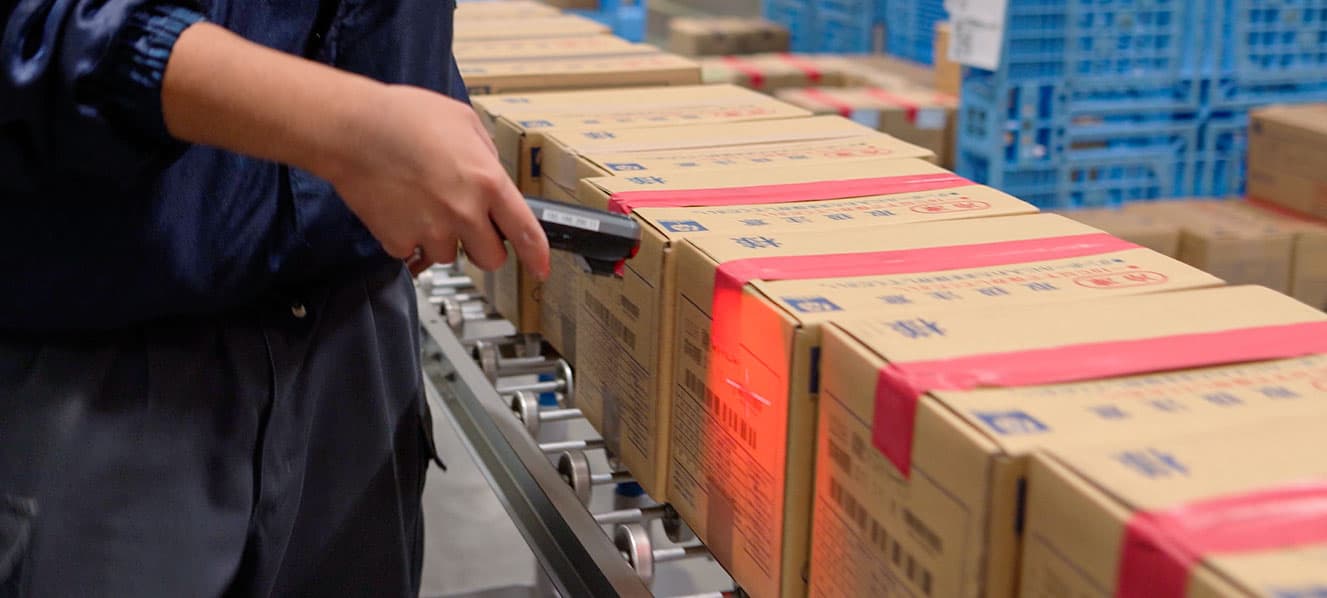
02.ハンディターミナル
商品のバーコードスキャン用に導入。ノートPCとBluetooth接続を行っている。ハンディターミナル故障に備え、Bluetooth対応リングスキャナでも代用できるよう設定済み。
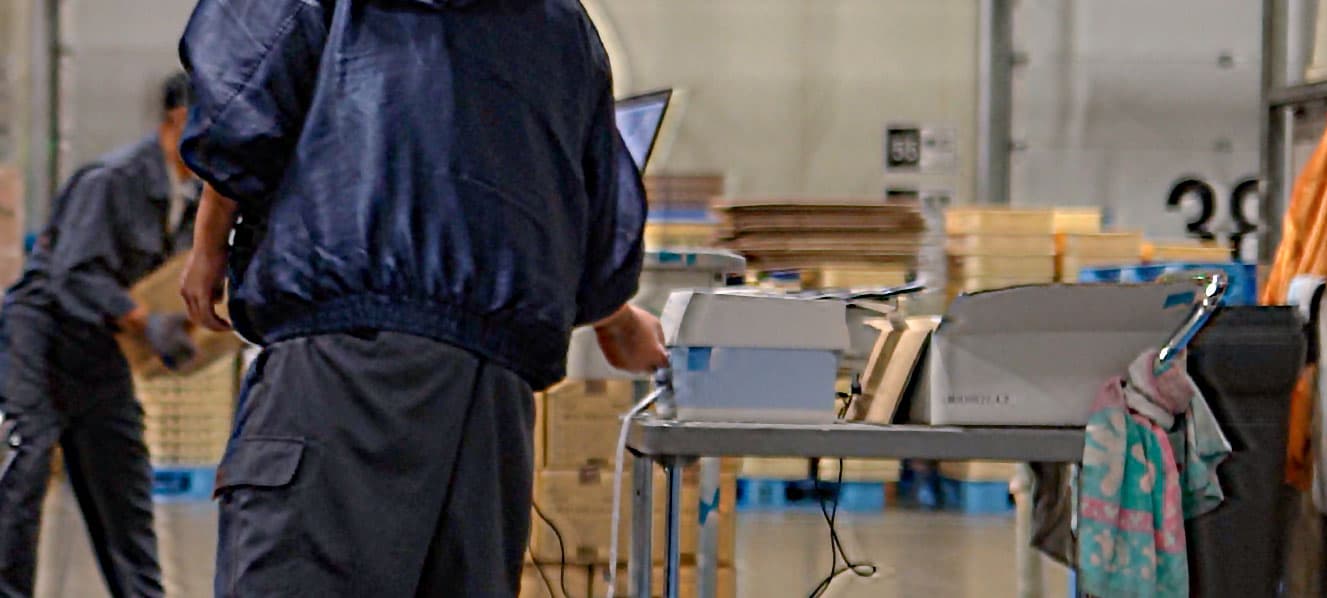
03.ラベルプリンタ(剥離方式・無線LAN対応)
商品へのラベル貼付のため導入。剥離方式のため、片手で貼り付けができ、台紙とラベルを剥がす手間がない。また、台紙の処分にも困らないメリットがあり、導入を決定。
システム開発
VisualStudio+SQLServer2016+MultiLABELISTV5にて自社開発を行った。
システム上の流れ
- 1.荷主様から受信した出荷依頼CSVを食品急送DBへ変換後格納
- 2.バッチ別数量リスト(店舗別)を発行し、数量を元に店舗エリアの大きさを決める
- 3.発注数量確認リスト(商品別)を発行し、大口納品エリアの大きさを決める
- 4.店舗納品カンバン(店舗別)を発行し、店舗エリアに掲示する
- 5.現場ノートPCにてラベル発行プログラムを実行しバーコードスキャン~ラベル発行までを行う
※作業現場で何か調べたいことが出てきたら、現場ノートPCのラベル発行プログラム上で様々な角度から検索及び確認が可能。